Moving Beyond BIM – Part II
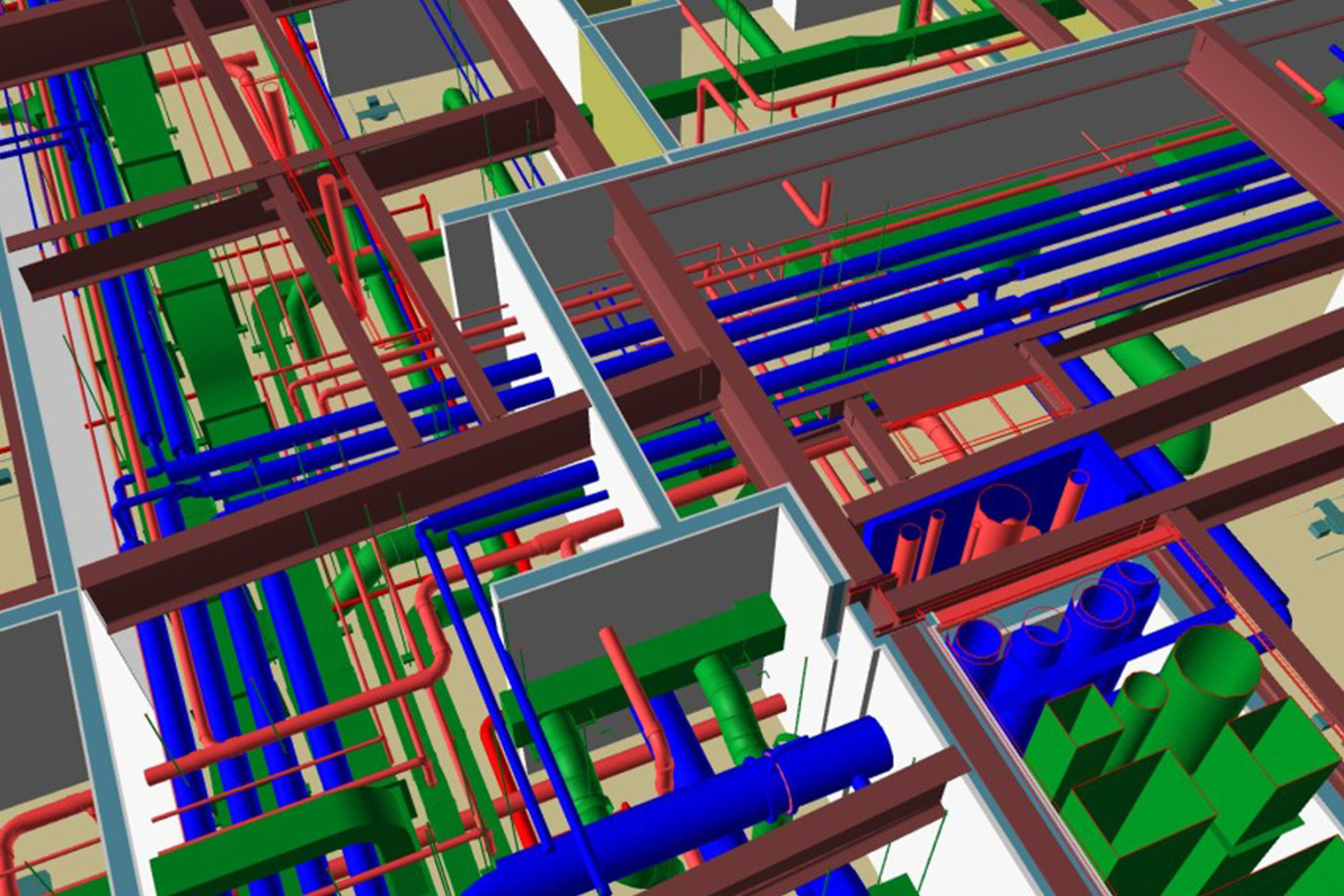
As promised, here’s more about our new firm, Prefix DfMA.
First an example of DfMA (design for manufacturing and assembly) in full practice. Ray O’Rourke, Owner of Laing O’Rourke has been a professional hero since we were introduced in 2010 in London by Paul Morrel, the UK’s Chief of Construction.
Laing O’Rourke is a leading UK and worldwide construction and fabrication company. He is–they are–the world’s top practitioners of DfMA. Look him up, then look up…with me. Ray started us thinking deeply about direct to fabrication and more.
The Explanation – Part II
This May, TOCCI acquired and launched a free-standing division called “Prefix DfMA”. My partner is Clayton Lyons. I’ve known Clayton for 15 years and he’s the most amazing MEPFP professional because he’s worn every hat necessary to be a ‘master mechanical’ and more. He’s been a licensed union plumber. He helped set up 2 of the largest mechanical fab shops in the Northeast (Cannistraro and American). He worked as an engineer at BR+A and RWS. For more than ten years was head of coordination for a top national CM. Heck, he even worked as a modeler of architecturally notable buildings (Eero Saarinen and Paul Rudolph for Gwathmy Siegel) where he fastidiously modeled gear-formed split rib concrete for the joy of the trying.
Back to BIM
We’ve loved Revit since we opened the shrink wrap on R1.5 (I think) in 2003. But we also learned (hated?) its limitations fast. It was never great at the bookends – the beginning (conceptual design) or the end (fabrication detailing). Yes, it undeniably owns the middle. Over the past 15 years, time and again we hit the limits of the tool and the limits of reasonable contractor expectations. Yet we still craved more engineer-modeled detail.
- Super-early selection of BIM-schmart subcontractors via IPD or deep design assist, or
- Put your head down, finish the 100% documents with your engineer and seriously adjust most of them later.
As to option 1, in this hyper-inflated market Owners are understandably reluctant to commit to early, non-competitive purchasing. So we have… 3D disposable design. Hey? Why call it disposable design? Yes, I suppose that’s unfair – the design itself is almost always good and the intent clear enough to price. But those “100% docs” contain precious little accurate geometry and practical routing because the stuff* simply isn’t where it needs to be. So, before starting any work, much of the designer’s beautiful 3D work must be deleted and redrawn**. Of course, with complex buildings like labs and hospitals “God is in the details” – as Mies van der Rohe once said (speaking of MEP Shop drawings***). Actually, this is where demons live too: 20% wasted effort (RFI’s/ASI’s), 15% labor rework, and the Owner’s worst exposure to change order claims.
Could it be our industry is crying out for a new profession? The DfMA design partner? Is it possible to get expert digital MEP craft involvement during design without crashing the bank? And if so, why can’t design handoff happen at the shop door? Why should it take 5 or 6 months – or even a year to make designs buildable when it’s time to build right then? If the answer is ‘yes’ to a new profession, Prefix may be one of the first.
When we come back next time we’ll explain Prefix’s people, specific tools and processes which ease design schedules, pre-coordinate complex systems and double offsite MEPFP prefabrication – all while reducing the number of MEP change orders by more than 70% and reducing design time and requests for additional services. Yes, sounds wild.
John Tocci, Sr.