Acknowledging Lean Design in Construction
Share
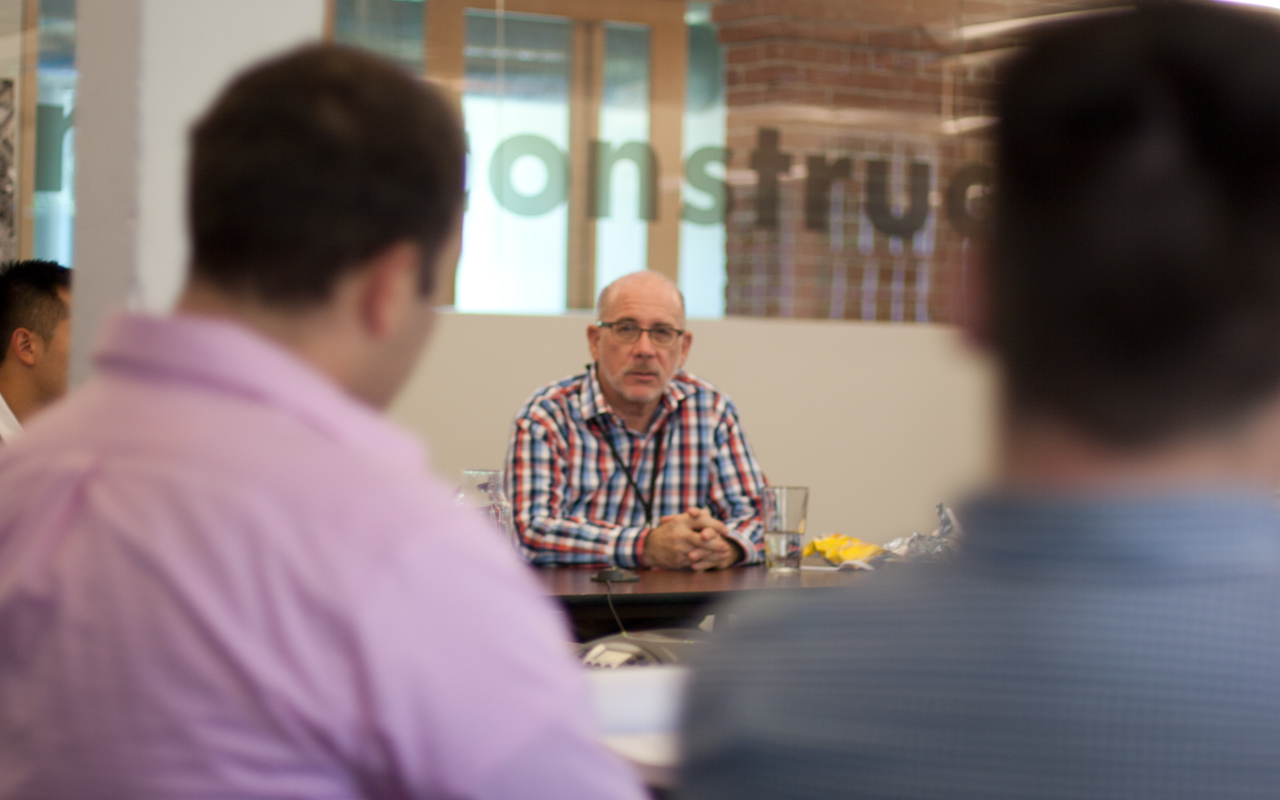
The point of Lean Design and Construction is to acknowledge that the building industry is inherently wasteful.
Recognizing this is the first step towards remedying it. A perfect construction project would have ZERO waste, ZERO transportation of products, 100% recycled or biodegradable materials and NET ZERO energy requirements. Suffice to say, there is no perfect construction project and it is unlikely there ever will be one. However, that doesn’t prevent us from emphasizing that some methods and some decisions lead to more waste than others. Why are we transporting granite quarried in Spain, shipping it to fabrication plants in Brazil and then bringing it to Boston to install? What was the plan there? Give a world tour to chunks of solid earth?
Tocci Project Manager Mark Herstein, pictured above leading a lean design + construction training session, drives the point home:
Most team setups for lean production are missing a simple ingredient: A lean management system!
You need a map if you are trying to get the team to a destination. What is the team striving to achieve? Once established you then need set benchmarks for how to achieve the identified goals. Provide solid examples of methods that are consistent with this approach and identify practices that are in conflict.
Lean management practices are easy to grasp and understand but difficult to sustain and consistently execute.
There will be many who will hear the concepts of Lean construction and then disregard it, some will hear it and try to adopt it but old habits will creep back, or immediate and convenient excuses will arise and they will forget about Lean practices. But, hopefully, there will be still others that will apply Lean construction methods and will use it so consistently that others recognize the value of the strategies and adopt them themselves.
Lean Implementation requires understanding between an organization’s culture and its management system and how each of the organization’s members contributes to the effort.
A company can pitch and describe how they are environmentally sensitive; how they care about the Earth and preserving it for future generations, but making the principle a reality is left to the people who WORK for this company. The company, “Tocci Building Companies” is not a building. It is not a building with Executives. It is not a building with Executives and Managers. It is a building with Executives, Managers, Superintendents, Assistant Managers, Assistant Superintendents, Estimators, Project Secretaries, Project Accountants, Business Development and Marketing People, Field Engineers, Laborers. In varying degrees each of these people need to contribute to the philosophy that the company professes – if the Company is truly adopting this principle. This means that the estimators need to ask lean questions when bidding a project. Operations staff needs to ask lean questions when awarding a project. Field personnel need to confirm that the subcontractors and suppliers are living up to lean principles their companies professed and agreed to at the onset of the project.
- Where did this product come from?
- Can it be produced locally?
- Can it be produced with different and easily replenishible materials?
- Can it be pre-fabricated to reduce installation time?
- Is there a more cost effective alternative?
In time, these questions change industries. Subcontractors hear these questions and think “they’re right, why shouldn’t we buy this product from a local source?” Suppliers hear these questions and think “they’re right, why shouldn’t we make this product with a different material?” These lessons will then be reused on all or many of their future projects. Simple questions with solid answers providing a lasting impact.
Lean management system sustains and extends gains from implementing lean production and practices.
The proper utilization of lean management systems imbeds itself in multi-dimensional methods and thereby becomes even MORE impactful. There is a train of suppliers, as suppliers have suppliers. As each one practices a more responsible lean methodology, the entire supply train is improved and savings are multiplied. Similarly, transportation of these materials is considered and improved. Ultimately, the system reaps the combined advantage of multiple layers of concerted effort to think “lean”.
Lean cultures grow from robust lean management systems.
As these systems bear fruit, other agencies and companies recognize and adopt these practices and they communicate it to associated industries. Practices familiar to the few outliers become mainstream and are consistently approved in manner and method. The escalated impact becomes second nature to all along the supply chain and then methods for lean adoption occur at levels and in a manner never even initially considered. Guess what? At that point we will all be well on our way to making a perfect building.