6 Reasons to “Go Modular”
Share
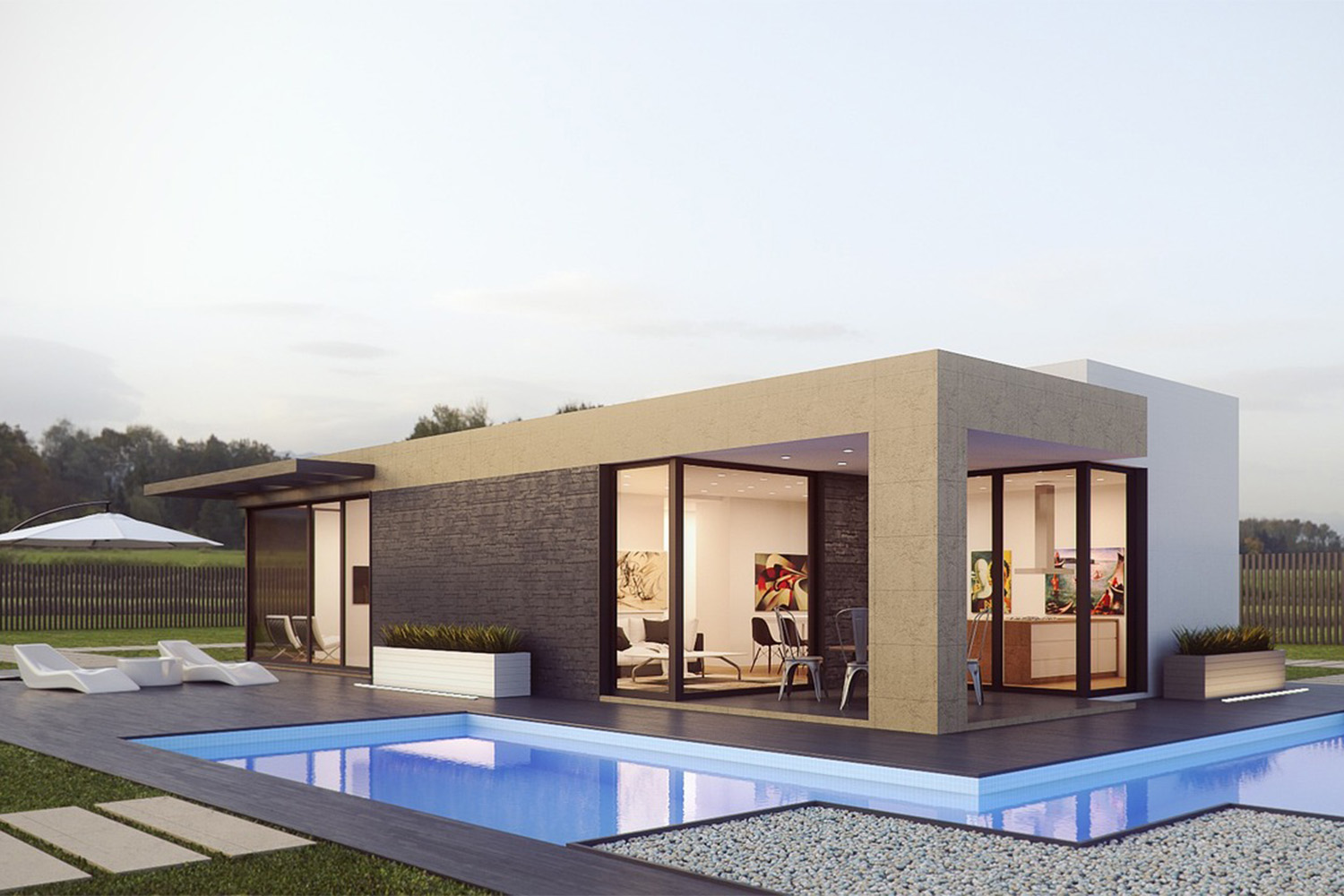
The following came out of a conversation between Joe Ferolito and VJ Tocci…
Today’s modular isn’t what your father remembers as modular. I remember the shaking and the echoing of older modular buildings, as I walked through them and knocked on walls. The quality of today’s modular construction is every bit the same as conventional. In fact, it’s better.
- Condensed Construction Schedule: On Chelsea Place, a recent modular project, we completed the entire 56-unit apartment complex in nine months. Conventional construction would have required twelve months (minimum). The 80 modules were installed in nine days followed by siding, roofing, interior MEP connections, elevator installation, landscaping, and the final punch within eleven months.
- Disruption Mitigation: This offsite construction process DRAMATICALLY minimizes noise and obstructions to neighbors. Face it, 9 days of disruption beats 5 or 6 months. The truth is you’ll likely have a bunch of spectators taking photos of the crane hoisting the 12 or 14 boxes per day as they’re installed, too amazed to complain.
- “No time for Change Orders” – because of the need to pre-approve all elements since they are being assembled and installed offsite, there is an inherent advantage (or disadvantage, depending on your perspective) because by the time “boxes” start arriving – it’s too late to make any changes. Think of custom ordering your Cadillac – if you wanted the “bone colored, hand stitched, leather seats” during your order – you better want it when it arrives, because that’s what you’re getting.
- Factory Advantage: Modules are constructed in a protected environment with single provider fabrication. A level of product consistency is assured and there isn’t a learning curve for new crews. No weather impacts, no inconsistent products because of inconsistent labor crews, and no discrepancies in trade scopes.
- Environmentally Friendly – Per modular companies, they factor a “1% waste”, yes – I said a ONE PERCENT WASTE. Typical construction waste amounts to 37% of materials used. This means two things: 1) you aren’t paying for material ending up in a landfill and 2) you aren’t filling landfills! As a side note – on Tocci’s both modular and conventional job sites, we recycle up to 75% of the construction waste by utilizing disposal partners that know how to recycle.
- Improved Sound Barrier – Both perimeter and interior walls are constructed more sturdily to accommodate transportation. Module walls are double-thick assemblies, as are the assemblies between floors due to individual transport. But the effective advantage is that there is twice the sound insulation WITHIN THE SAME UNIT.
The reality is that modular construction is NOT less expensive than conventional construction (except in Union and Prevailing Wage conditions). However, it is significantly more efficient and delivers projects “to market” in dramatically less time. This delivery enhances the developer’s pro forma and can be the difference between meeting your target market and missing it.
Goodbye, we’re done – go get building. But wait – first tell us about your positive and negative experiences with modular. Leave a note in the comments.